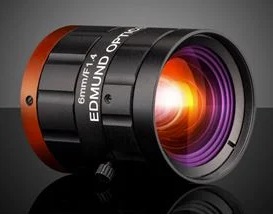
Ideal when paired with SONY IMX990 or SONY IMX991 sensors, Edmund Optics’ C-Series fixed focal length SWIR lenses support a 2.8µm pixel pitch far smaller than classic SWIR pixel sizes in the 5 – 15µm range.
Fixed focal lengths help the lens designers achieve great performance while minimizing production costs due to fewer parts.
Industry-insider tip
Certain sensors marketed as Vis-SWIR (Visible plus SWIR spectrum coverage) are far less expensive than those traditionally designed for SWIR alone – and perform really well in the SWIR range (900 – 1700nm). The SONY IMX990 and SONY IMX991 are two such sensors, the former available in AVT Goldeye 130, and the latter in AVT Alvium 1800. So are SONY IMX992 and SONY IMX993, as featured in AVT Alvium cameras with diverse interface options.
So while certain users buy those sensors for applications that generate an image in both the visible and SWIR portions of the spectrum – MOST buyers are purchasing these sensors “just” do do SWIR applications in a cost-effective way.
It’s a bit like buying a dual-function toaster oven and never using one of the functions – but if it creates a valuable solution for you, who cares about the feature not used?
Edmund Optics saw the opportunity to create a lens series for the customers using the sensors referenced above to do dedicated SWIR applications. So they created their C-Series fixed focal length SWIR family, with 7 members, and focal lengths from 6 – 50mm.
Did we mention performance?
Recall that lens performance is typically expressed by the Modular Transfer Function (MTF). Below is the MTF chart for the 6mm FL at 1.3µm wavelength, from the Edmund Optics C-Series fixed focal length lenses. All 8 members of the family show comparable performance – see spec sheets for details.
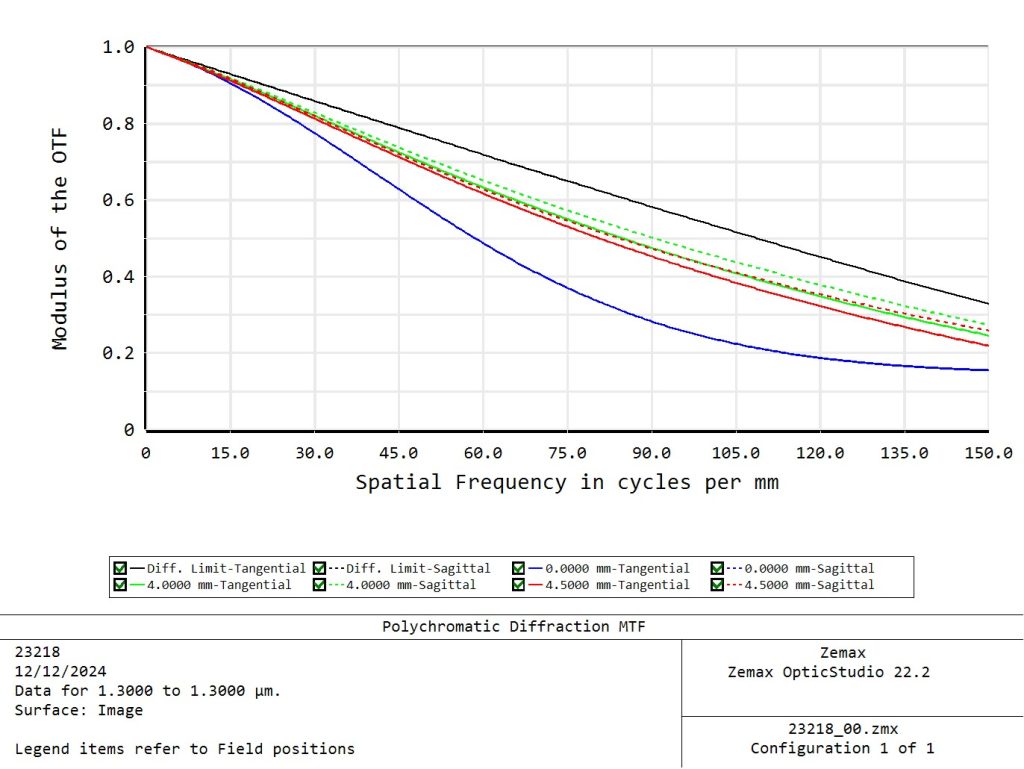
Shorter focal lengths not always easy to find
With fixed focal lengths at 6mm, 8.5mm, 12mm, 16mm, 25mm, 35mm, and 50mm, knowledgeable customers may note that especially the shorter focal length offerings are not that common in the machine vision optical market.
Compact and cost-effective
As fixed focal length lenses, each member of this lens series only need a focus adjustment – fine tuning – which is lockable against vibration slippage. They do NOT need the complexity of a varifocal lens. That means fewer glass elements and less metal, yielding a smaller form factor, handy if space is an issue.
It also means the lenses are less expensive to manufacture, a savings the user can enjoy in achieving a cost-effective way to get good performance in the SWIR spectrum.
Built as a variation on another lens series
It’s worth noting this SWIR-optimized lens series piggybacks on Edmund Optics visible spectrum C-Series fixed focal lenses. The key difference is the new lens series are optically coated for the SWIR spectrum. The benefit to the user is that Edmund Optics could do a spin on an existing lens series, which is cost-effective for the customer as well.
Optimized for factory automation applications
Both the visible and SWIR versions of the C-Series lenses have been optimized with factory automation in mind, particularly with respect to WD, size, and cost.
1st Vision’s sales engineers have over 100 years of combined experience to assist in your camera and components selection. With a large portfolio of cameras, lenses, cables, NIC cards and industrial computers, we can provide a full vision solution!
About you: We want to hear from you! We’ve built our brand on our know-how and like to educate the marketplace on imaging technology topics… What would you like to hear about?… Drop a line to info@1stvision.com with what topics you’d like to know more about.