Unpacking the μEye SCP/ μEyeSLE product names to preview what’s on offer, the “S” stands for Streaming. The rest of the product names come from IDS Imaging’s popular GigE Vision camera families μEye CP and μEye LE, respectively. So the value proposition is a bundled streaming solution piggybacked on top of another product platform. This creates economies of scale for the manufacturer and the customer alike.
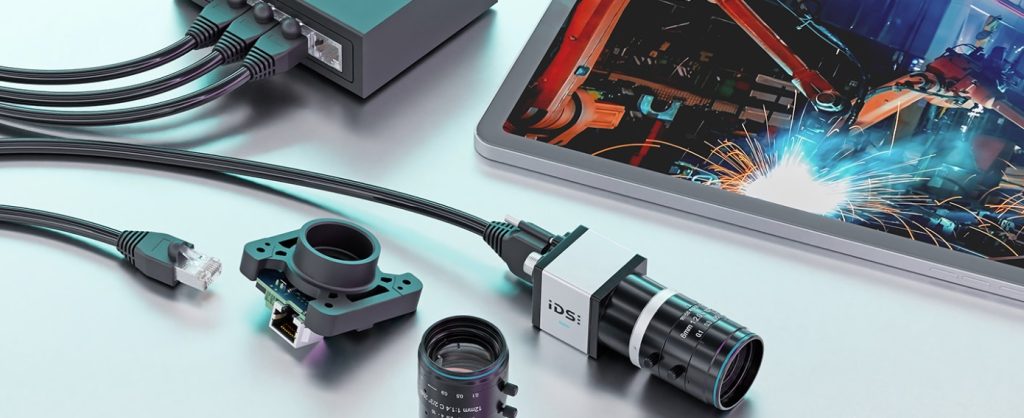
Continuous monitoring with event-triggered video recording
Anybody running complex systems has to monitor them for performance and quality control – and/or to recover from breakdowns or detected concerns. Traditionally one had two options:
- Wait for a breakdown and try to deduce what went wrong, or
- Construct a video monitoring system from the constituent components… and program as needed
The “wait and see” options is attractively inexpensive on the face of it. But it risks expensive losses from the period prior to detecting the failures. Worse, it may not be possible to determine what went wrong if one missed the event that triggered the failure.
Constructing a video monitoring system from scratch is possible – and many have done it. Until now it generally required sourcing camera, lens, and PC, and writing complex software capable of episodic streaming and recording, and event-detection and logging.
IDS μEye SCP / μEye SLE provide Plug’n Stream no-PC-needed solution
Systems evolution in many fields, including machine vision, periodically takes what once had to be programmed to something that need only be configured. The system provider helpfully packages the algorithms into parameterized controls that are user-friendly to the deployer. That way one can focus on the application domain, event management, and process control.
IDS Imaging has done exactly that to create μEye SCP / μEye SLE – think “industrial dashcam” – with both housed and board-level options. The comprehensive 9 minute video below provides a great introduction to the product, its capabilities, and some applications examples.
The comprehensive 9 minute video below provides a great introduction to the product, its capabilities, and some applications examples.
Event Recording
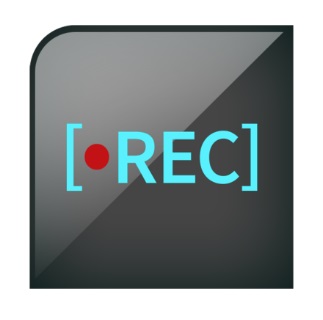
The system streams continuously to internal persistent memory, periodically overwriting previous streams that were not part of any events deemed worth saving. This creates a recorded stream for a defined period from x seconds prior to an event, through the event, and to y seconds afterwards, where x and y are user-definable.
That documents machine malfunctions or failures. Which makes it easier to analyze process errors – and address them for system improvement.
No PC needed – System on a Chip (SoC)
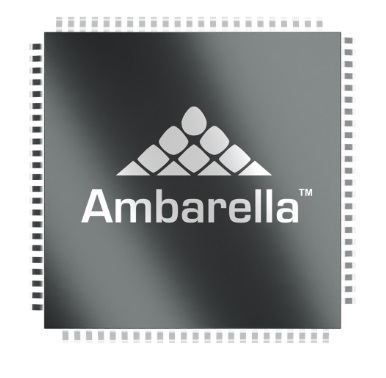
With System on a Chip (SoC) from Ambarella, the camera has the onboard smarts to directly process and evaluate image data.
The user need only configure the parameters that define an “event”, the duration to capture before and after the event, which of several formats to record, and whether to operate standalone or integrated into other systems.
Use cases
Just to get the juices flowing, consider use cases like the following:
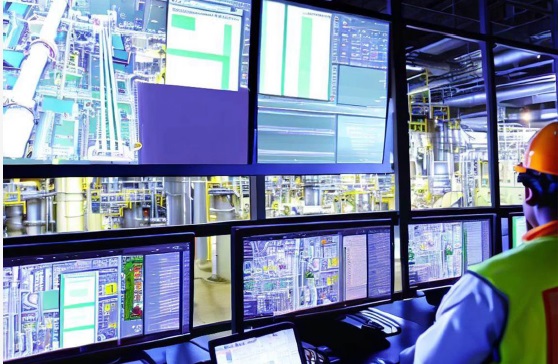
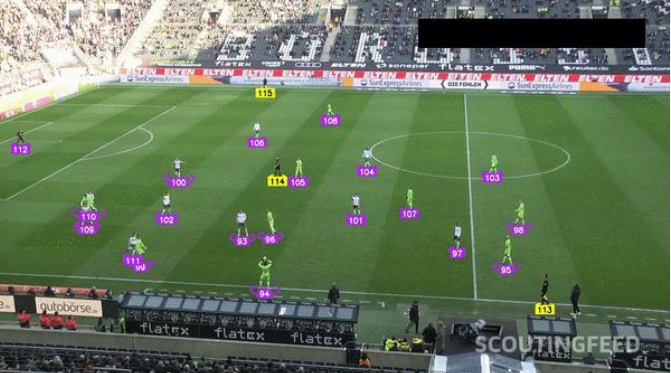

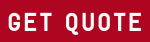
WebCockpit configuration
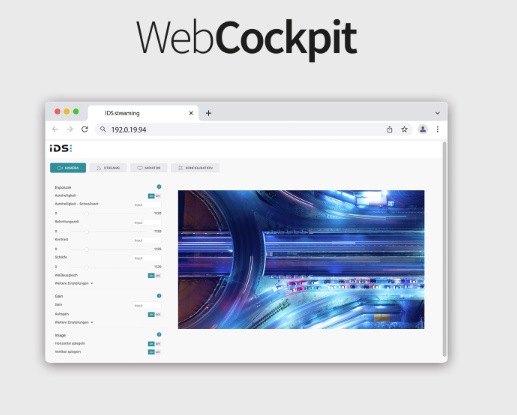
With no PC required to operate the system in standalone mode, configuration may be done through a frontend in the browser. The frontend settings control streaming, recording, and video modes.
Optionally on can use the web service and a REST API to seamlessly integrate into existing systems, for those who prefer or require integrate over standalone deployments.
1st Vision’s sales engineers have over 100 years of combined experience to assist in your camera and components selection. With a large portfolio of cameras, lenses, cables, NIC cards and industrial computers, we can provide a full vision solution!
About you: We want to hear from you! We’ve built our brand on our know-how and like to educate the marketplace on imaging technology topics… What would you like to hear about?… Drop a line to info@1stvision.com with what topics you’d like to know more about.