JAI has over 60 years experience in the vision industry, and is likewise a longstanding part of the 1stVision portfolio. JAI produces a diverse range of cameras, including area scan and line scan; across multiple interfaces; and spanning visible, NIR, SWIR, and UV portions of the spectrum.
In this article we announce six new line scan camera models: 4 in the Sweep series at 4k each; and 2 in the Sweep+ series at 4k and 8k respectively. There’s a niche for every model.
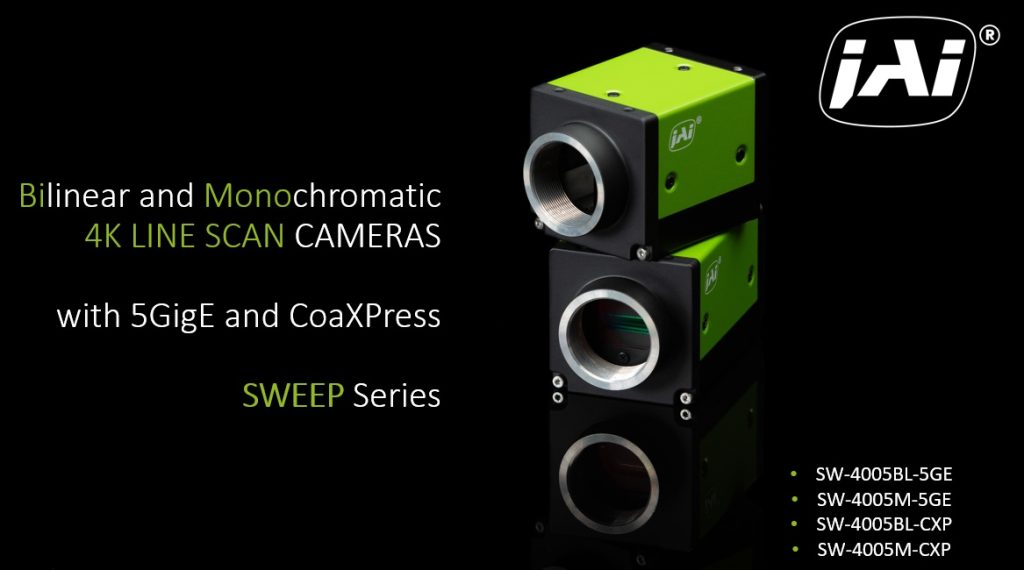
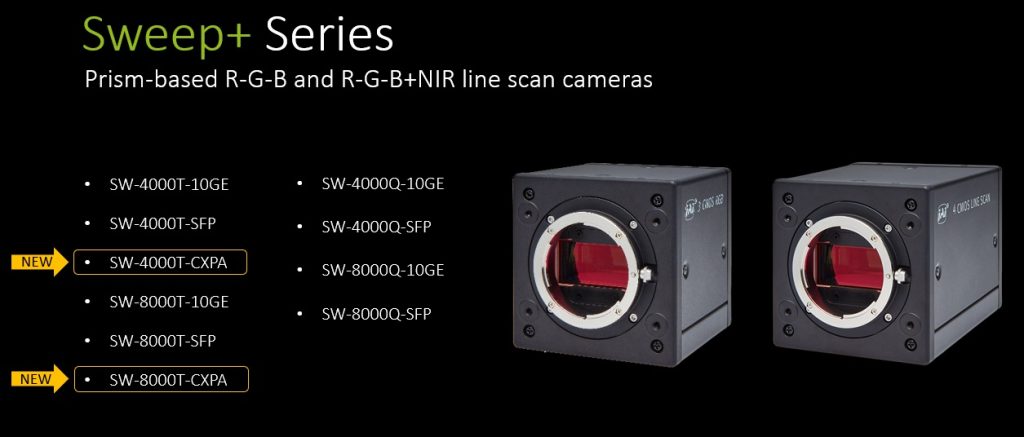
Four new 4k line scan Sweep models; Two new Sweep+ models incl. 8k
At the risk of information overload, we’ve bundled this product release update of six new camera models across two product families into a single article. We hope the reader appreciates the compare-and-contrast approach as a way to understand the value proposition for each camera/family.
When you need line scan it’s nice to have options
While area scan sensors with big 2D pixel array outputs are right for some applications, line scan is a better fit for others. In particular, if the object being imaged is essentially continuous, line scan can be an effective way to take narrow image slices with a lower cost 1D sensor that’s long in just the dimension that maps to the object width. Movement of the object (or sensor) together with successive slices then creates the second dimension.
The 1stVision Knowledge Base offers illustrated articles on line scan topics, including How to Calculate Line Rate Based on Conveyor Speed and Polarization Techniques with Line Scan Cameras. Now on to the new camera models!
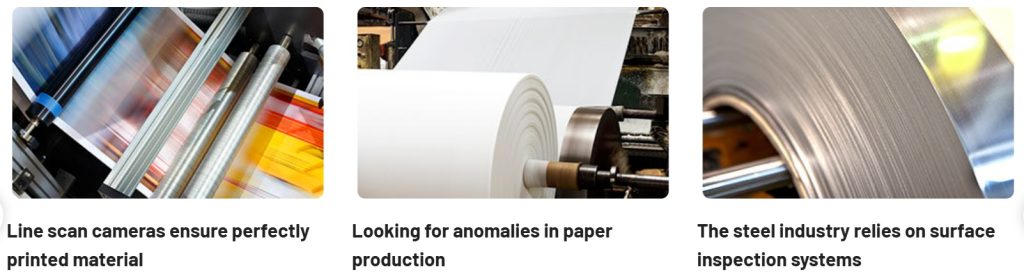
JAI’s Sweep line scan cameras vs. Sweep+
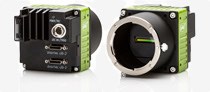
JAI’s Sweep line scan cameras include a wide offering of monochrome, bilinear, and trilinear models, at 2K, 4K, 8K, and 16K. Interface options include 5GigE, 10GigE and CoaXPress. If you need color sensing, the bilinear approach is an affordable approach, and often plenty good enough. For true color capture, the trilinear sensors are superior – if needed.
Sweep+ cameras, as suggested by the + suffix, are JAI’s top of the line color and multispectral line scan products. The beam-splitter prism optics, together with three (color only models) or four (color plus NIR) sensors, deliver high-precision color resolution. Due to the data volumes generated, the Sweep+ cameras use CoaXPress, 10GigE, and CameraLink interfaces to achieve line rates suitable to the respective sensor sizes and anticipated applications.
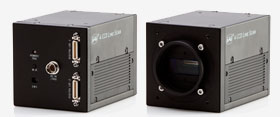
Mini-tutorial on single sensor vs. multi-sensor color imagin
While Bayer filters or equivalent provide single sensor color, that’s good enough for some applications, there is some loss of color resolution via that inherent physical interpolation. So demanding applications take advantage of separate sensors for each segment of the spectrum, using a prism to separate wavelengths. The resulting camera is physically larger to accommodate the the prism, extra sensors, and electronics – but the best possible color performance is achieved.
A deeper dive on the new Sweep cameras
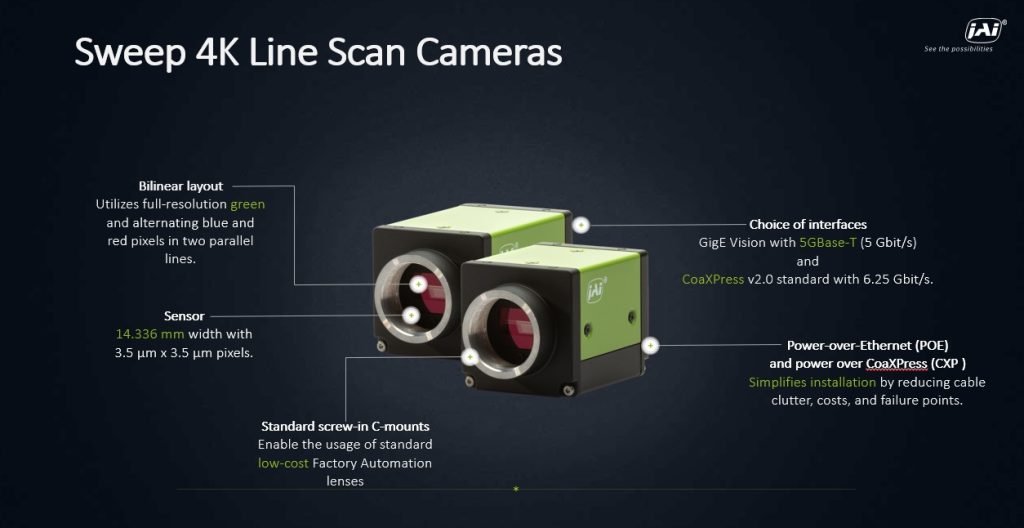
Monochrome line rates are 2x that of the bilinear color models
… because there is a single monochrome pixel mapped to the target object’s corresponding area.
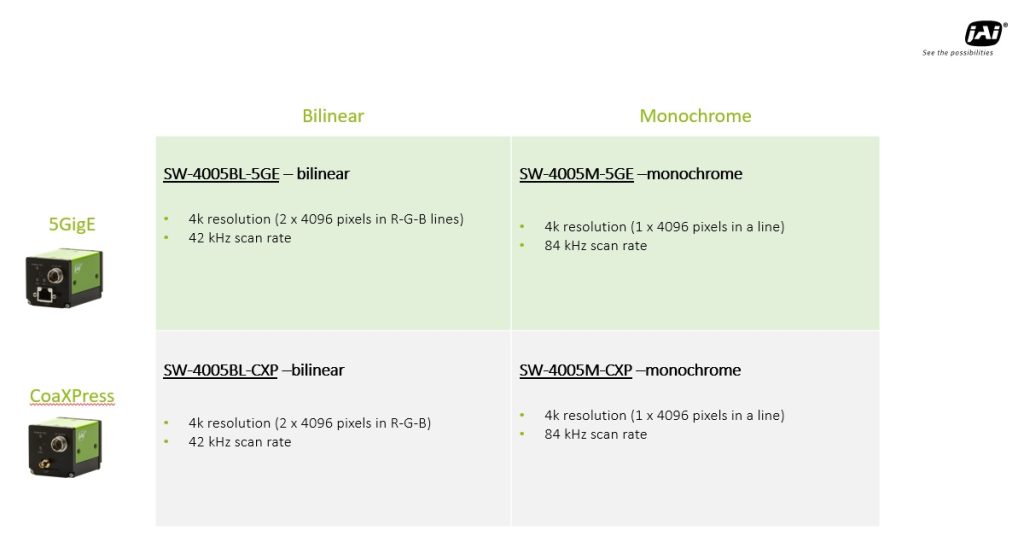
But if you need color the bilinear approach is an efficient way to do it, since there are only two rows of data transmitted for every real-space row imaged….
A peak at the bilinear approach to color line scan imaging
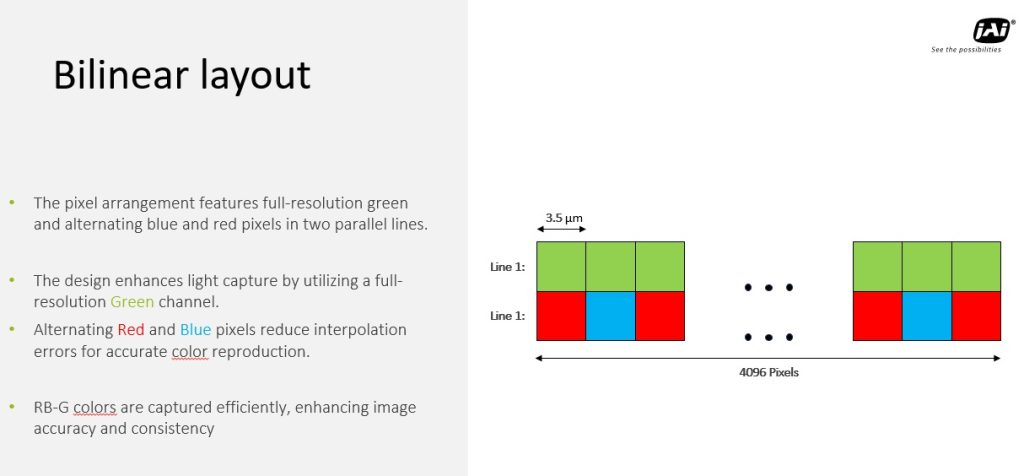
Other JAI Sweep camera features
Keystone correction, aka tilted view correction, onboard the camera
Trigger-width dynamic exposure control
Resume-scanning control for stop-start motion
Trigger delay
… and more
Drill in to JAI Sweep camera models and datasheets. Or let us guide you.
More details on JAI’s new Sweep+ line scan cameras:
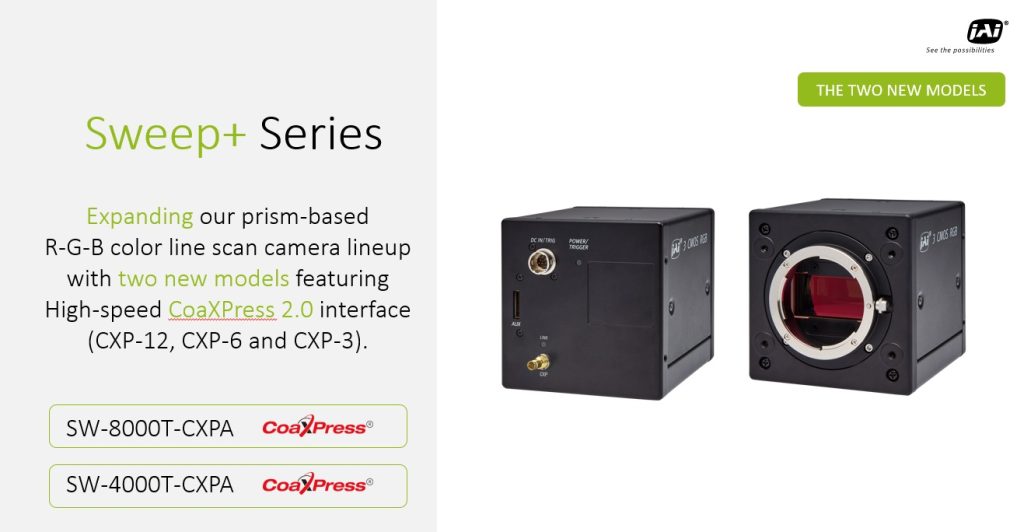
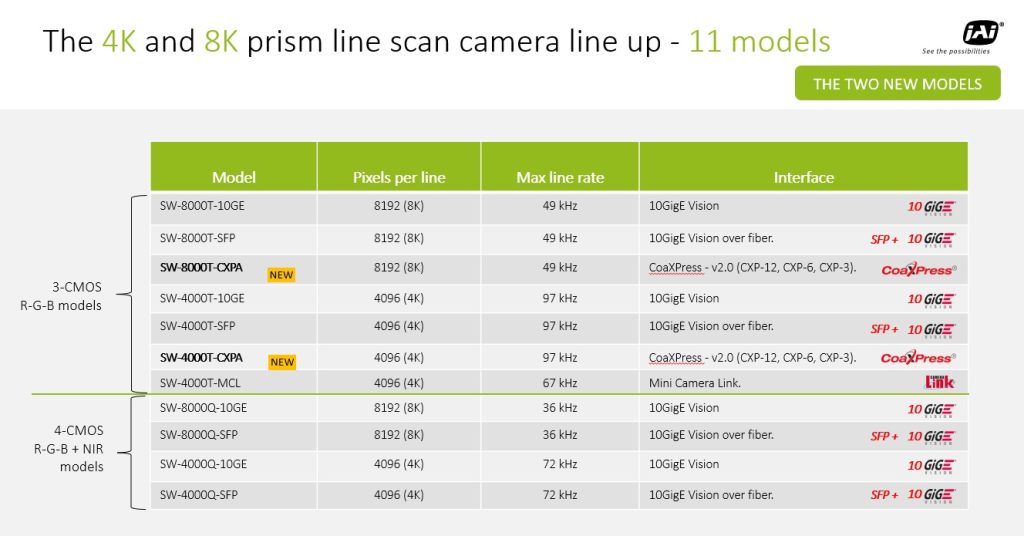
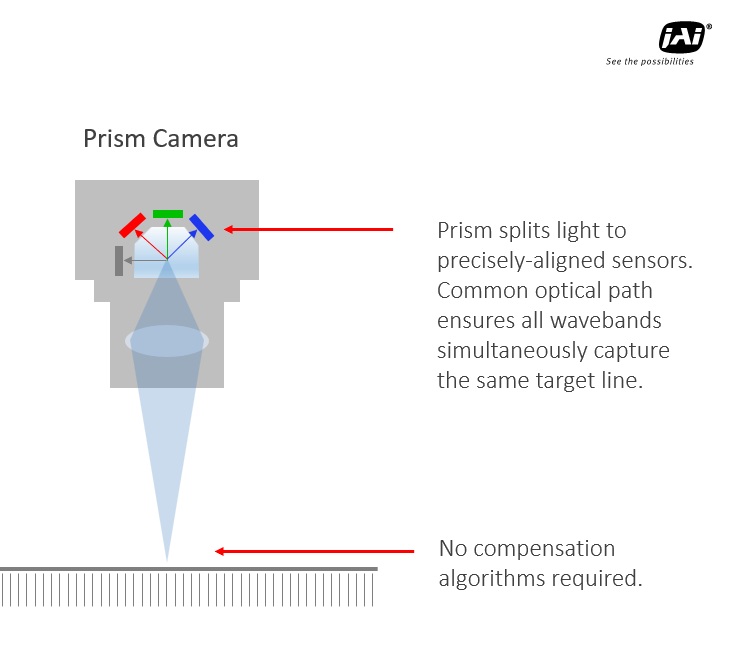
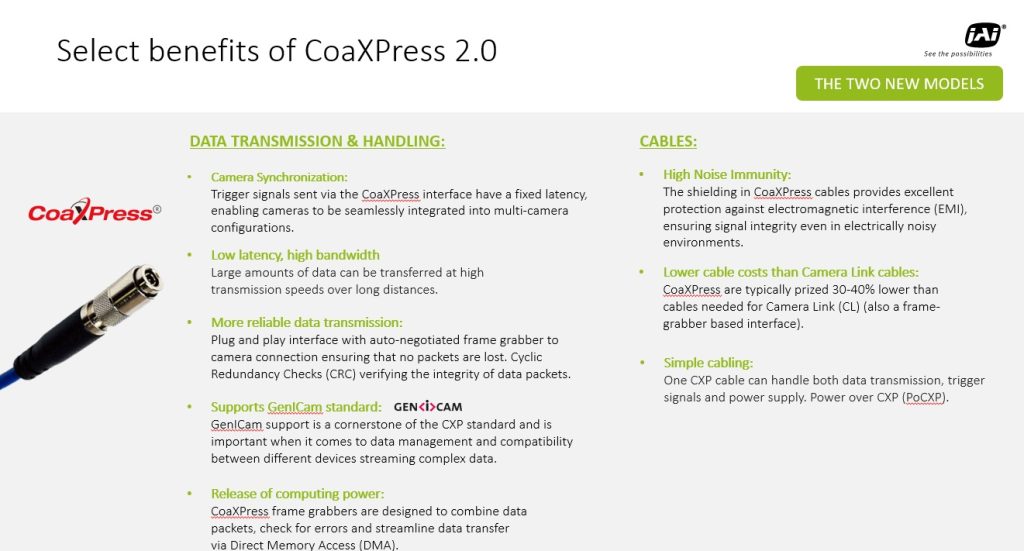
And yet more features…
You get the idea… Sweep+ is a remarkable camera family. There are even more features to find in the Sweep+ product details and datasheets. Or just call us at 878-571-5683 for expert assistance. Tell us about your application requirements and we’ll guide you to an optimal camera. Lighting, lenses, filters, cables, and software too.
1st Vision’s sales engineers have over 100 years of combined experience to assist in your camera and components selection. With a large portfolio of cameras, lenses, cables, NIC cards and industrial computers, we can provide a full vision solution!
About you: We want to hear from you! We’ve built our brand on our know-how and like to educate the marketplace on imaging technology topics… What would you like to hear about?… Drop a line to info@1stvision.com with what topics you’d like to know more about.