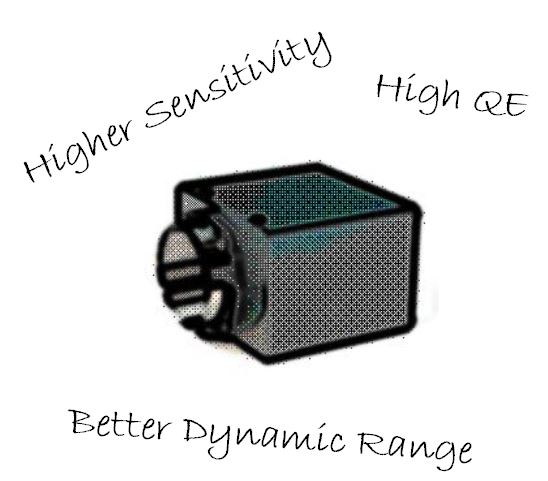
Industrial machine vision cameras historically have used CCD image sensors, but there is a transition in the industrial imaging marketplace to move to CMOS imagers. Why is this?.. Sony who is the primary supplier of image sensors announced in 2015 it will stop making CCD image sensors and is already past its last time buy. The market was nervous at first until we experienced the new CMOS image sensor designs. The latest Sony Pregius Image sensors provide increased performance with lower cost making it compelling to make changes to systems using older CCD image sensors.
What is the difference between CCD and CMOS image sensors in machine vision cameras?
Both produce an image by taking light energy (photons) and convert them into an electrical charge, but the process is done very differently.
In CCD image sensors, each pixel collects light, but then is moved across the circuit via current through vertical and horizontal shift registers. The light level is then sampled in the read out circuitry. Essentially its a bucket brigade to move the pixel information around which takes time and power.
In CMOS sensors, each pixel has the read out circuitry located at the photosensitive site. The analog to digital circuit samples the information very quickly and eliminates artifacts such as smear and blooming. The pixel architecture has also radically changed moving the photosensitive electronics to be more efficient in collecting light.
6 advantages of CMOS image sensors vs CCD
There are many advantages of CMOS versus CCDs machine vision cameras outlined below:
1 – Higher Sensitivity due to the latest pixel architecture which is beneficial in lower light applications.
2 – Lower dark noise will contribute to a higher fidelity image.
3 – Pixel well depth (saturation capacity) is improved providing higher dynamic range.
4 – Lower Power consumption. This becomes important as lower heat dissipation equals a cooler camera and less noise.
5 – Lower cost! – 5 Megapixel cameras used to cost ~ $2500 and only achieve 15 fps and now cost ~ $450 with increased frame rates.
6 – Smaller pixels reduce the sensor format decreasing the lens cost.

What CMOS image sensors cross over from existing CCD image sensors?
1stVision can help in the transition starting with crossing over CCDs to CMOS using the following cross reference chart. Once identified, use the camera selector and select the sensor from the pull down menu.
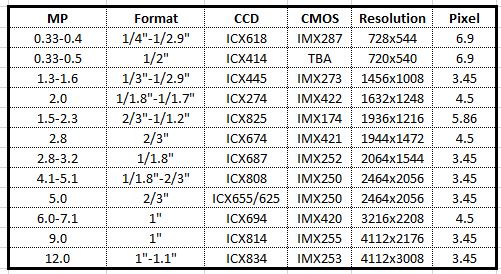
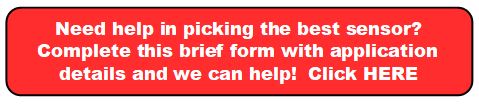
1st Vision’s sales engineers have over 100 years of combined experience to assist in your camera selection. With a large portfolio of lenses, cables, NIC card and industrial computers, we can provide a full vision solution!
Ph: 978-474-0044 / info@1stvision.com / www.1stvision.com
Related Blogs & Technical resources